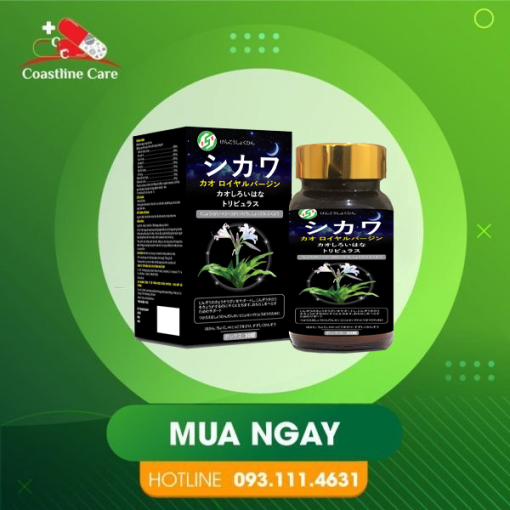
This can be much more typically observed in producing procedures that could practical experience considerably less interaction with mom nature or processes that do not need continuous measuring or refinement.
They can be named following Japanese engineering professor Kaoru Ishikawa from the nineteen sixties, who assisted use them to producing procedures.
To assist construction the solution, the categories are sometimes picked from one of the widespread styles shown beneath, but may well arise as some thing exclusive to the applying in a selected case.
The lighting may be a contributing cause, but it really really should not be the primary a single investigated. The Ishikawa diagram needs to be expanded every time 5 Whys is utilized. For example, the department could end up as substance → element not installed → staff skipped operation → do the job setting as well dim → inadequate lights → mild bulbs burned out.
You can even use the scientific system in the form of the very well-recognized approach-do-Check out-act (PDCA) cycle to empirically investigate the failure. Generally, failure investigations begin with brainstorming doable triggers and listing them within an Ishikawa diagram. This isn't essentially Improper, but normally the Concepts listed tend not to lead into the failure beneath investigation.
Learn about production defects, prevalent leads to, And just how manufacturers can put into practice the most effective techniques nha thuoc tay to prevent defective products and solutions.
The diagram might be utilized to depict management's speculation on what happened and make clear how the condition could be solved.
They're form-hearted and prepared to support their buddies. They are sometimes innocent or unaware in risky scenarios. They wish to consume chocolate and onions.
The defect or trouble is demonstrated as being the fish’s head on the ideal facet (ordinarily). The major types or results in of the situation or defect will be the ribs from the fish’s backbone.
Sorting potential causes into distinct groups causes it to be simpler to discover root will cause later on. You need to use the 6Ms as a place to begin that will help you choose nha thuoc tay key varieties.
You can use paper checklists or spreadsheets to determine the issues or use distinct equipment for example SafetyCulture (formerly iAuditor) to capture and organize your specified challenges.
They resemble a fish skeleton, While using the "ribs" representing the will cause of an party and the final outcome showing at the head with the skeleton. The objective of the Ishikawa diagram is to permit administration to select which difficulties ought to be dealt with in order to acquire or keep away from a certain function.
An Ishikawa (or fishbone) diagram really should be established once the trouble assertion is prepared and knowledge has long been gathered. An Ishikawa diagram need to be seen like a graphical depiction of hypotheses that can describe the failure below investigation.
Common uses of nha thuoc tay the Ishikawa diagram are product design and quality defect avoidance to discover prospective elements causing an overall influence.